Since our artisans are the reason we do what we do, we’d love to take some time to give a bit of background on the processes that our partnering villages use. In total, we offer three textile techniques: batik, weaving and embroidery, so let’s not waste any time and dive right into the batik process!
The handmade fabric featured in the Indonesia 6 textiles come from the artisan's hands of Surakarta, Indonesia. In the form of batik dyed cotton, these cool-colored works of art are a modern take on some very traditional techniques, both in batik fabric design and classic East Asian architecture.
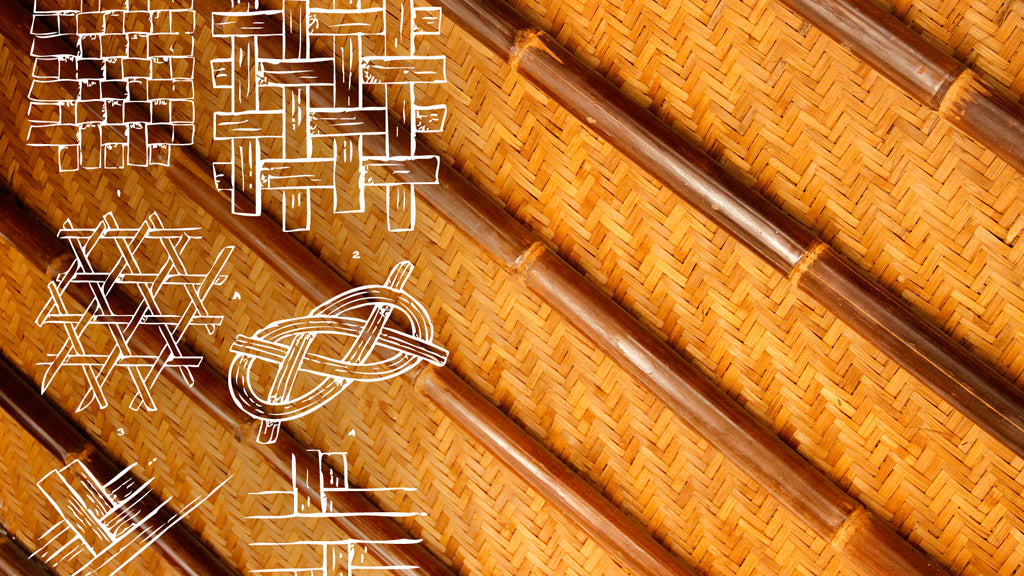
Woven reeds, palm leaves and wild grasses have been a multifunctional mainstay for most cultures from Peru to the Philippines. The design for the Indonesia 6 fabric came from this classic weaving style that is widely used in Indonesian architecture for roofs and walls, but mostly in floor mats called Tikan Pandan in Surakarta. These mats are rolled out every night at Warungs (small street-side cafe's) where people gather to eat late night snacks and drink tea. Let’s take a look at how they do batik, Surakarta style!
Batik copper stamps being made.
Step 1: Begins with a drawing, via pencil and parchment paper so there is some translucency, which is key for artists to trace their ancestor's designs allowing the copper stamp maker to then translate that into the tool.
Step 2: Is taking copper scraps and magically bending them into form to match the artist's drawing. It's mind blowing how they do this! Copper strips manipulated with pliers, hammers, shears, picks and files, true craftsmanship!
Step 3: The artist comes to do a quality control check to make sure the copper craftsman's tool matches his/her drawing.
Step 4: The approved or adjusted tool makes its way onto the wax stamper's shelf.
Step 5: Is all about reduction... The "batik chef" who knows the precise recipe for the batik wax, melts the wax so the stamper can apply the wax to the cotton fabric.
Step 6: The stamper then takes the artist's and coppersmith's tool, dips it in the chef's wax and ever-so carefully applies it to the virgin cotton fabric. Now that the wax has been applied and has seeped into the fibers of the cotton it is ready for the next step.
Step 7: The cotton fabric is then bathed in dye.
Step 8: Is the easiest of all, hang it out to dry!
Step 9: We gather Ethnotek customer orders and then place a bulk fabric order with the artisans.
Step 10: Once the fabric arrives at the ETK workshop in Vietnam, it is sewn into finished Ethnotek bags with tender love and care.
Step 11: These hot new items are ready to ship to you!
Step 12: The cycle is now complete! When you buy a bag with these fabrics, it supports artisan employment for the continued creation of them, which in turn, helps preserve the culture that is literally woven and stamped into every piece. You can then wear your bag with pride, knowing the story behind it and lovely people who made it by hand.
Did you know?! Our Ghana fabrics employ the same beautiful batik technique! The main difference is that instead of a copper block, they use wood.
A block of wood about the size of a human hand is shaved smooth by a machine so it has a perfectly flat surface. (Some blocks are left square on top and some have handles carved into them.) Then the intricately designed Ghanian motifs are carved into the block using chisels, knives, and files.
Hand carved wood blocks for stamped batik.
Both batik and tie-dye were introduced to Ghana from South East Asia in the 1960s. They grew popular from the middle 1960s to the late 1970s. The patronage of this fabric declined significantly in the 1980s due to various reasons some of which include a preference for a cheaper alternative import. It has however seen a revival in recent years.
Early African tie-dye involved a lot of spots and specks on the designs. They tied as well as stitched the fabrics to achieve a look different from the rest of the world. Other techniques such as painting and splashing the wax onto the fabric before dying is unique to African batik.
Additional techniques are used in conjunction with block printing, such as painting and splashing wax on before dying.
Batik has been used as an industry to alleviate poverty in rural areas alongside other textile making art forms. Due to the fact that small startup capital is required to establish the business, many women have set up businesses from their homes producing very brilliant and colorful designs for the local and international markets. We couldn't be more proud to be a part of this process!
Our partnering artisans in Ghana make their textiles in 25 meter sections and we purchase them according to the amount of customer orders we get from our Tribe each season. The bigger the Tribe grows; the more chances the people of Ghana have to express their creativity!
---------------
So that's it folks! I hope you enjoyed this deep-dive and now know a bit more about the batik process than you did before. "If you have any questions about these processes, be sure to leave a comment!"
- The Ethnotek Team